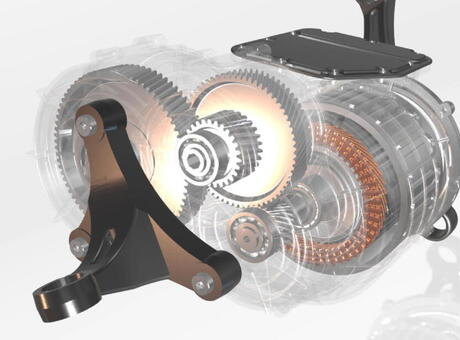
Fill in the form to have a Dassault Systèmes expert contact you to answer your questions and discuss any of your needs.
As the world moves towards smarter products, faster time to market, and sustainability, it is vital that we revisit traditional approaches to product development. Advanced design, modeling, and simulation functionalities are poised to transform the product development process, meeting the needs of a future economy. Know more about the possibilities with integrated modeling and simulation here.
The electric drive constitutes a critical component for the electrification of vehicles and hence the electro-mobility strategy. A complex system in its own right, the electric drive needs to be integrated into both the electric powertrain and the full vehicle. Gaining early insights into system interdependencies using Model-Based Systems Engineering (MBSE) is key to achieving the best possible performance for competing design objectives. It enables tight integration of design and simulation activities, including connecting system simulation with physics simulation.
Multiphysics simulation enables engineers to predict and verify the system performance across multiple design objectives and in all possible operating scenarios. However, many of the disciplines are competing and finding the best trade-offs is a challenge. The teams need a collaborative environment that allows them to optimize designs by simultaneously taking into account thermal and mechanical requirements, electromagnetic performance, durability, noise and vibration control, as well as lubrication requirements.
Dassault Systèmes offers best-in-class solutions for electric drive engineering within a collaborative environment.
Today’s organizational challenges are highly complex with the necessity to deliver variety of product variants with a shortened development cycle and cost pressures. Our solutions enable to address these complex challenges by providing accurate multi-scale and multi-physics simulation solutions. Leveraging simulation early in the design phase can help to reduce development time, reduce the cost of physical testing, and reduce the risk of not meeting certification requirements. We deliver high fidelity simulation solution of various physics such as structures, fluids, multibody, and electromagnetics scenarios directly linked with the product data. Modeling, simulation, and visualization technology are fully integrated on the 3DEXPERIENCE Platform facilitating rapid product design and development.
Additive manufacturing empowered by generative design is revolutionizing how production parts are being conceived and produced. A digital thread that connects, integrates and intuitively captures design, materials and manufacturing, is key for functional parts.3DEXPERIENCE, backed by multiphysics-based simulation, enables such a transformation through a unified and simplified interface. Provides designers, simulation analysts and manufacturing specialists a rich set of additive manufacturing applications for generative design, build planning, virtual print and shape compensation
With full integration of design and structural simulation on the 3DEXPERIENCE platform, our Structural Validation solution allows for simulation-driven decision making, ultimately leading to higher product performance and reliability. Easy propagation of design updates to all simulation analysts, direct reuse of design data in structural models – such as composite or fastener data – and automation of model creation tasks are key advantages of the seamless integration with design. The collaborative nature of the 3DEXPERIENCE platform enables multiple users or teams to simultaneously work on the creation of structural models for large sub-systems. These capabilities lead to significant improvements in engineering efficiency and accelerate the creation of large scale structural models from months to weeks.